Mono-Material Solutions
Mono-materialization is gaining attention as a way to make packaging easier to recycle. However, a major challenge is how to achieve the essential functions—such as preservation and strength—that were previously provided by multi-material packaging, using a single material.
The artience group is actively developing products that address the various challenges arising from mono-materialization and is working to promote the shift toward mono-material packaging.
Challenges of Mono-material Packaging
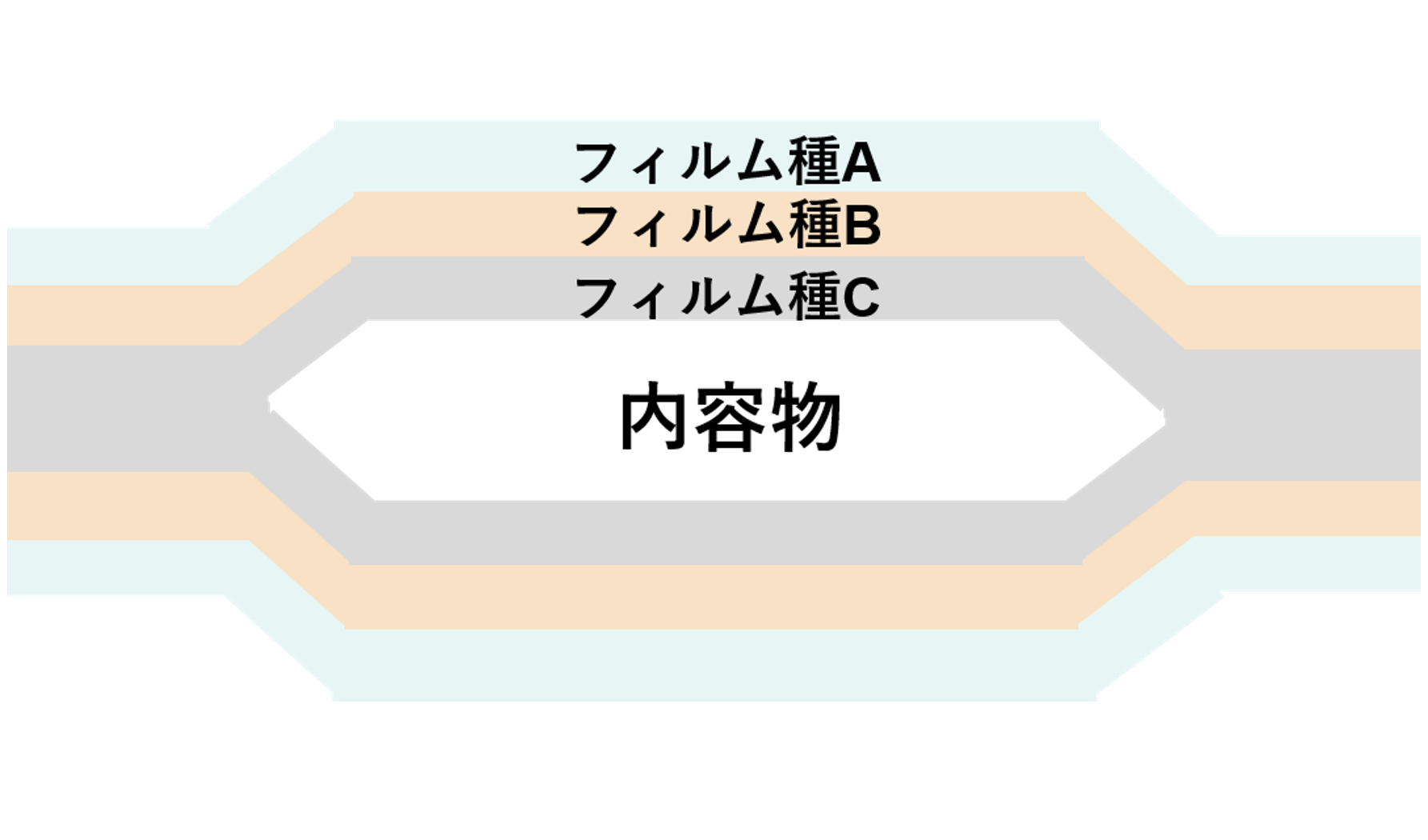
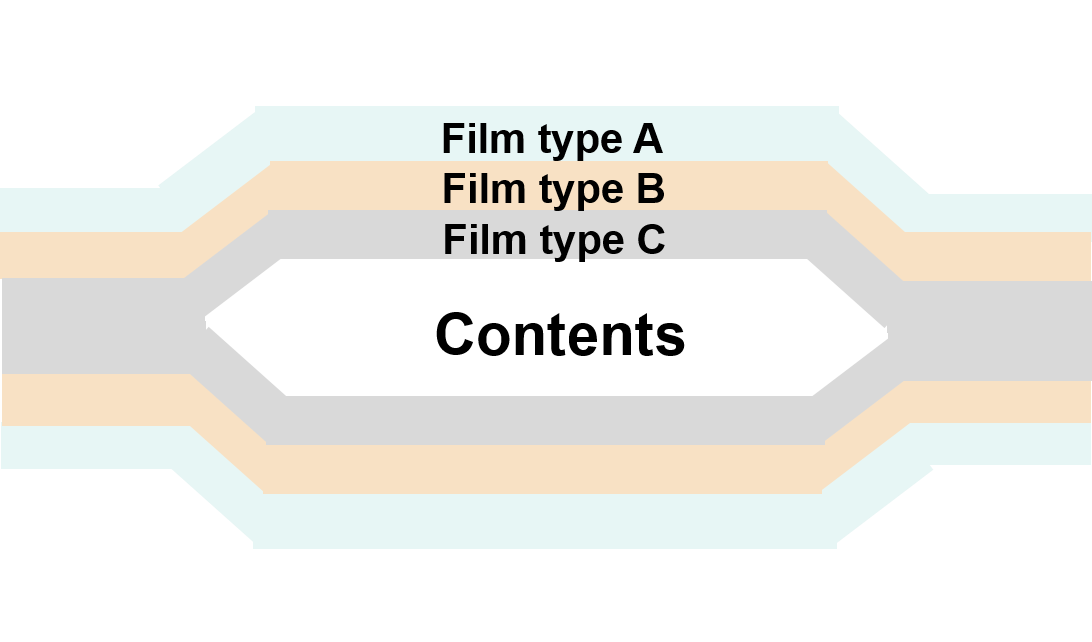
Mono-materialization offers a solution to this problem.
By converting multi-material packages into those made from a single material, recyclability can be significantly improved.


In order to promote mono-materialization, it is essential to achieve the same functional performance required for packaging—previously realized through multi-layer films—using only a single material. However, changing the film structure can lead to insufficient barrier properties against unwanted substances or lower the melting point of the film, which may reduce production efficiency during bag making.
The artience group is developing products that maintain key functions such as preservation and strength, as well as production efficiency, while also enabling easier recycling during the reprocessing stage. Through these efforts, we are addressing the challenges associated with mono-material packaging.
Solutions Proposed by the artience group
Barrier coatingDesigned to inhibit oxygen permeation / Effective in preventing odor leakage
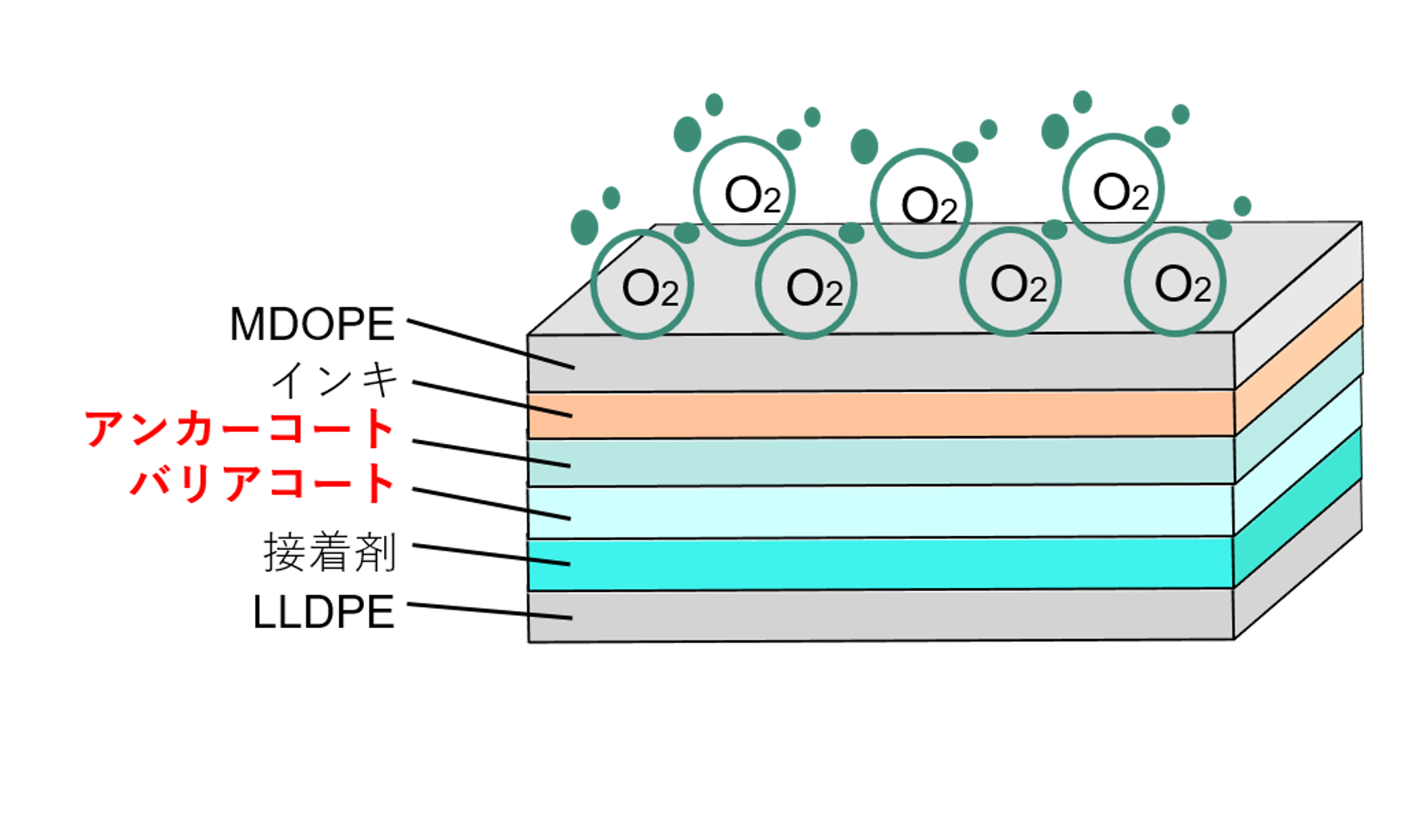
Traditionally, preventing oxygen transmission and odor leakage required the use of aluminum foil or multi-material packaging structures. Our barrier coatings, however, deliver high barrier performance (oxygen transmission rate: ≤ 1.0 ml/m²·day·atm) without using aluminum foil, enabling mono-material packaging.
These coatings can be applied to a wide range of packaging films such as PE, OPP, PET, and NY, and the desired oxygen transmission rate (OTR) can be adjusted according to the coating weight. In applications such as food, daily necessities, and pharmaceuticals, our coatings not only protect contents from oxidation to maintain quality and safety, but also prevent odors from escaping the package.

Traditionally, preventing oxygen transmission and odor leakage required the use of aluminum foil or multi-material packaging structures. Our barrier coatings, however, deliver high barrier performance (oxygen transmission rate: ≤ 1.0 ml/m²·day·atm) without using aluminum foil, enabling mono-material packaging.
These coatings can be applied to a wide range of packaging films such as PE, OPP, PET, and NY, and the desired oxygen transmission rate (OTR) can be adjusted according to the coating weight. In applications such as food, daily necessities, and pharmaceuticals, our coatings not only protect contents from oxidation to maintain quality and safety, but also prevent odors from escaping the package.
Heat resistant coatingPrevents film deformation under heat for stable packaging performance
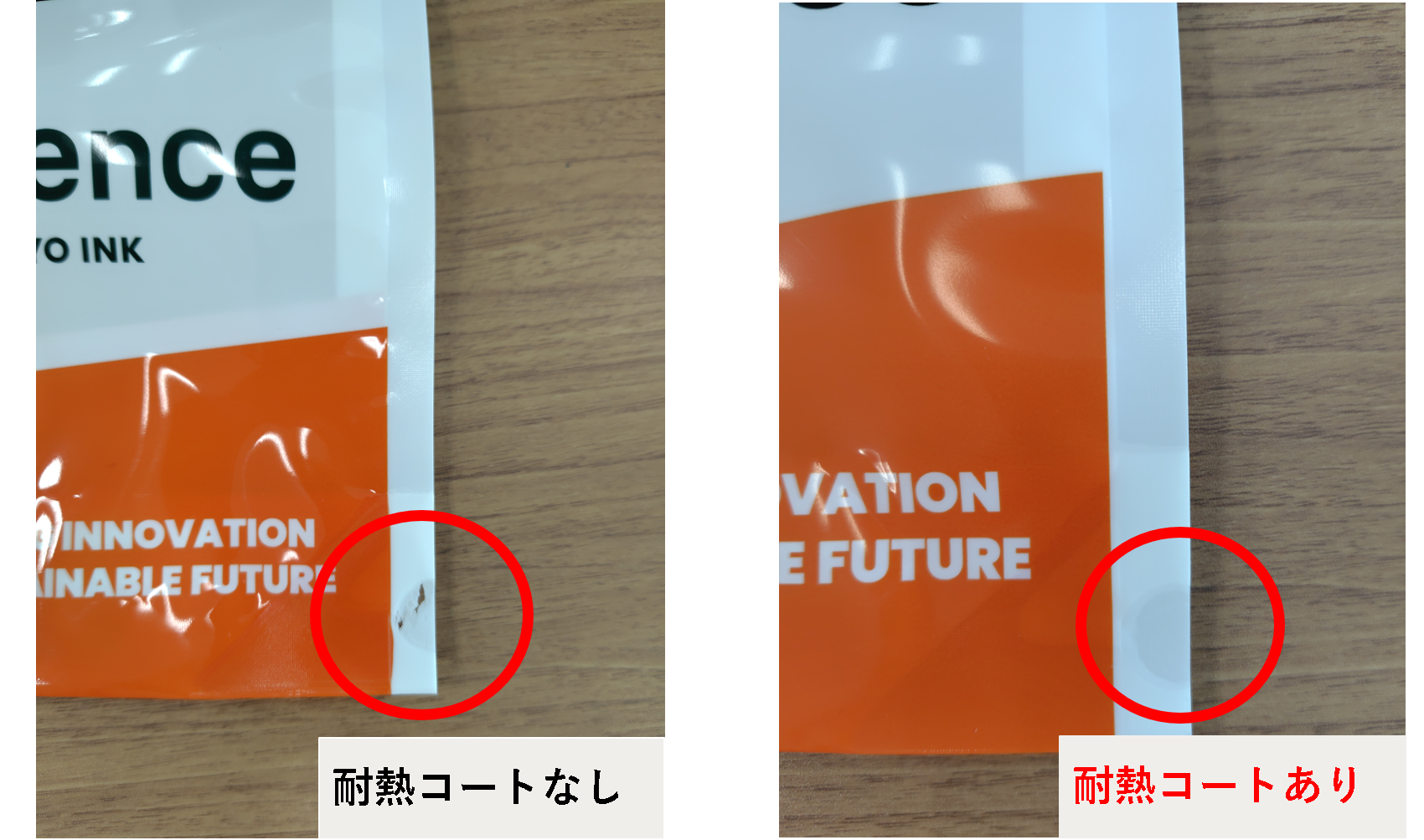
Typically, these issues are addressed by lowering the heat seal temperature, but doing so also reduces the bag-making speed, leading to a decline in production efficiency. By applying our heat-resistant coating agent to the outermost film layer, the heat-sealable temperature range can be expanded by approximately 20°C, helping to improve productivity in the packaging process.
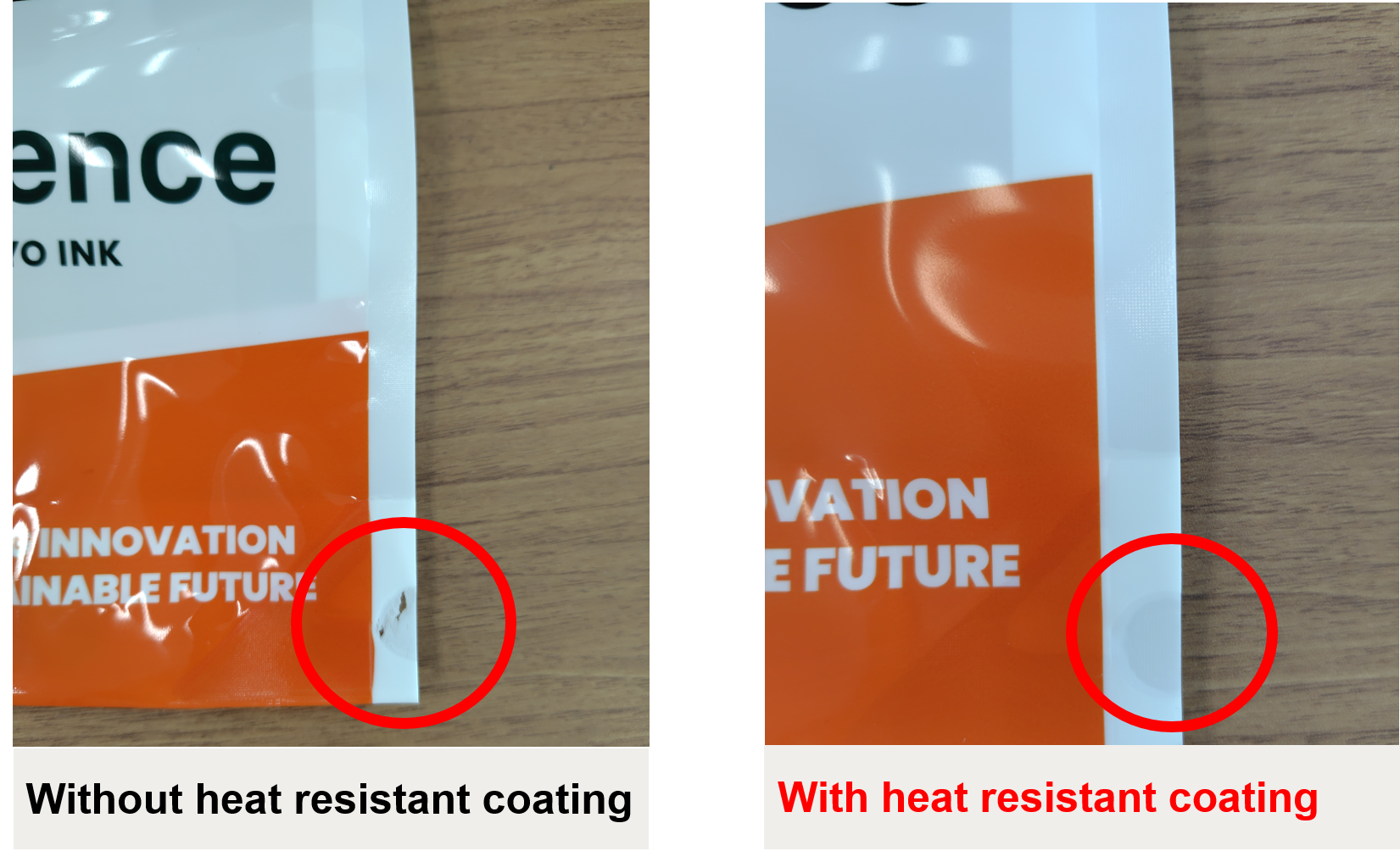
Typically, these issues are addressed by lowering the heat seal temperature, but doing so also reduces the bag-making speed, leading to a decline in production efficiency. By applying our heat-resistant coating agent to the outermost film layer, the heat-sealable temperature range can be expanded by approximately 20°C, helping to improve productivity in the packaging process.
Delamination & Deinking SolutionsFor removing inks and adhesives from films
In the recycling of plastic packaging, it is essential to remove printing inks and adhesives used on the surface and between the layers of films in order to obtain high-quality recycled plastic. This not only improves the purity of the recycled material but also expands its potential applications.
At the artience group, with Toyo Ink taking the lead, we have established technologies for deinking and delaminating inks and adhesives used in plastic packaging. Through these efforts, we are contributing to the improvement of recycled plastic quality and promoting more effective plastic recycling.
Inquiries
TOYO INK CO., LTD. Marketing Headquarters
TEL:+81-3-3272-7693